- 27 juin 2019
- En Wouter Verheecke
- | 5 min. temps de lecture
- | Source: Metallerie
NOUVELLE AUTOMATISATION SUR DES FRAISEUSES EXISTANTES
Uptime et flexibilité optimisés grâçe à la manutention des palettes de Liebherr
La société néerlandaise VDL GL Precision fabrique des pièces de haute précision sur ses deux fraiseuses 5 axes C50 de Hermle. Dans leur recherche d'une plus grande disponibilité et d'une plus grande flexibilité, ils ont remplacé les changeurs de palettes par un véritable système FMS de Liebherr. Ertec a géré l'ensemble du projet et était responsable de la livraison du premier système de ce type au Benelux. Marc Smits, manager operations chez VDL GL Precision, est d'ores et déjà convaincu des avantages: “Cela nous permet de produire plus, en étant plus flexibles et plus rapides, et donc de renforcer notre position sur le marché.“
ACTIVITES
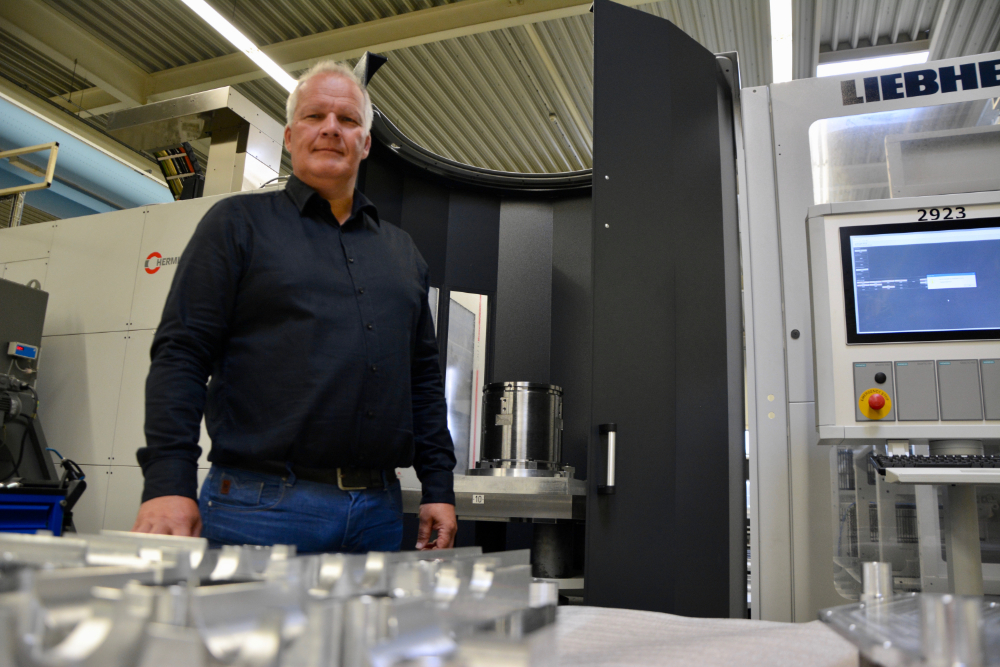
L'ancienne entreprise 'GL Precision' d'Eindhoven a été fondée il y a plus de cinquante ans par Gerard van der Leegte. Lorsqu'il a pris sa retraite en 2015, il a cédé son entreprise au VDL Groep. Elle était alors entre les mains de son frère, Wim.
Entre-temps, son fils Willem a repris les rênes de ce géant néerlandais de l'industrie métallurgique. VDL GL Precision, avec 103 sociétés VDL, fait donc maintenant partie de l'immense groupe.
Technologies de pointe
“Comme le nom de notre entreprise l'indique, nous produisons ici des pièces et des modules très précis, principalement pour l'aérospatiale, l'optique, l'industrie des semi-conducteurs et pour les applications scientifiques avec la technologie ebeam“, commence Marc Smits, manager operations.
FRAISEUSES
Beaucoup de ces pièces sont usinées dans une zone de production conditionnée à20 °C sur les deux fraiseuses 5 axes C50 Hermle avec chargement de palettes: les pièces maîtresses du parc machines.
6 positions de palettes
“Ces machines sont au service de nos clients depuis dix ans, à notre grande satisfaction. Elles fonctionnent avec beaucoup de précision et n'ont pas besoin d'être remplacés. Nous étions convaincus que nous pouvions en tirer davantage, alors nous avons planché sur la question“, explique M. Smits. “La limitation provenait de l'automatisation existante pour le chargement frontal. Les deux changeurs de palettes standard séparés n'avaient chacun que trois positions: deux à l'extérieur et un à l'intérieur de la machine. Vous êtes en grande partie dépendant du temps de rotation des produits à usiner. S'il ne s'agit que d'une heure chacun pour trois pièces différentes, cela ne représente que peu de travail fourni la nuit. Et c'est justement le problème, parce que nous ne travaillons pas en équipe ici. Il nous faut une automatisation poussée pour résoudre ce problème“, souligne le manager.
MANUTENTION DES PALETTES
La solution? Nous l'avons trouvée après quelques visites de salons et grâce à Ertec qui, en tant que fournisseur de machines, avait réalisé avec succès de nombreux projets d'envergure dans cette région.
24 positions de palettes
“Le PHS 1500 All-round de Liebherr, un système de manutention de palettes d'une capacité de 1.500 kg sert de remplacement. Le robot se déplace à une vitesse de 1 mètre par seconde entre les fraiseuses et le nouvel entrepôt de palettes, qui compte 24 positions: huit en largeur et trois en hauteur. Le nombre de postes a quadruplé, de sorte que nous pouvons désormais travailler pleinement pendant la nuit ou le week-end. En tirant le meilleur parti de ces heures sans opérateurs, nous pouvons utiliser pleinement les fraiseuses, exactement comme nous l'avions prévu. Le temps de disponibilité est beaucoup plus élevé et nous pouvons mieux gérer les produits à court terme“, dit-il.
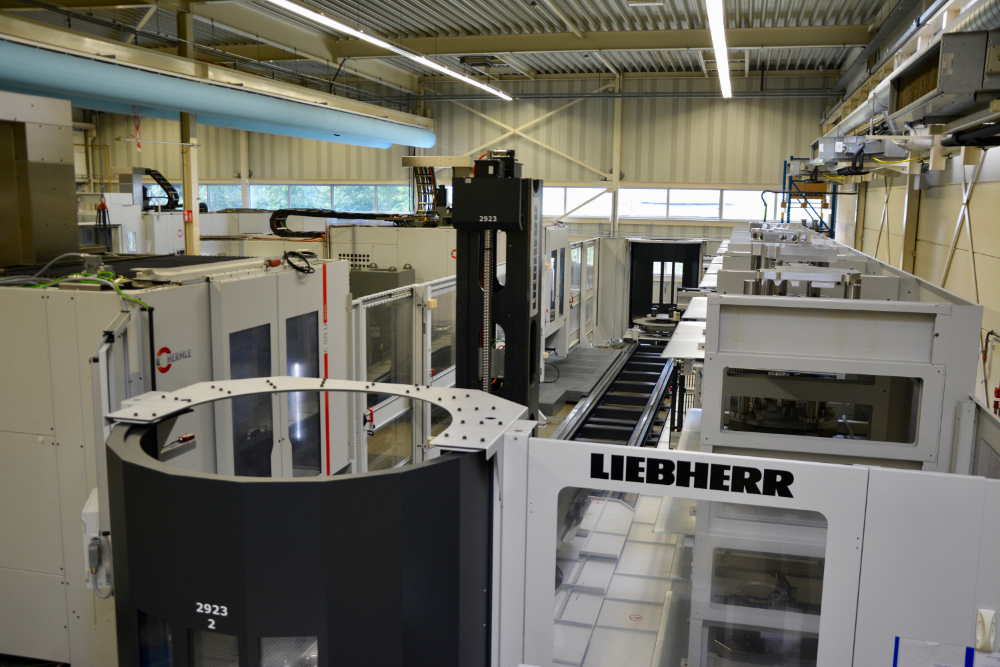
Flux de travail
Le chargement d'une nouvelle palette ou le déchargement d'une pièce à usiner s'effectue aux stations situées des deux côtés de la cellule. “Notre flux de travail ne nécessite plus qu'un opérateur à la commande numérique d'une fraiseuse six heures par jour, pour un travail précis. L'autre machine peut continuer à fonctionner automatiquement, pour des usinages moins exigeants. Pendant les deux heures restantes, l'opérateur effectue les travaux préparatoires pour le travail de nuit suivant, les deux fraiseuses étant alors continuellement en mode automatique“, explique Smits.
Barrière de sécurité
Pour permettre cette méthode de travail, l'installation standard devait encore être équipée de deux écrans de sécurité automatiques. “Un capteur de mouvement détecte la présence d'une personne entre le magasin et les fraiseuses, après quoi la barrière adaptée se déploie. Cela protège l'opérateur du robot, qui entre-temps peut continuer à se déplacer dans l'autre partie de l'installation“, poursuit le manager.
COMMANDE
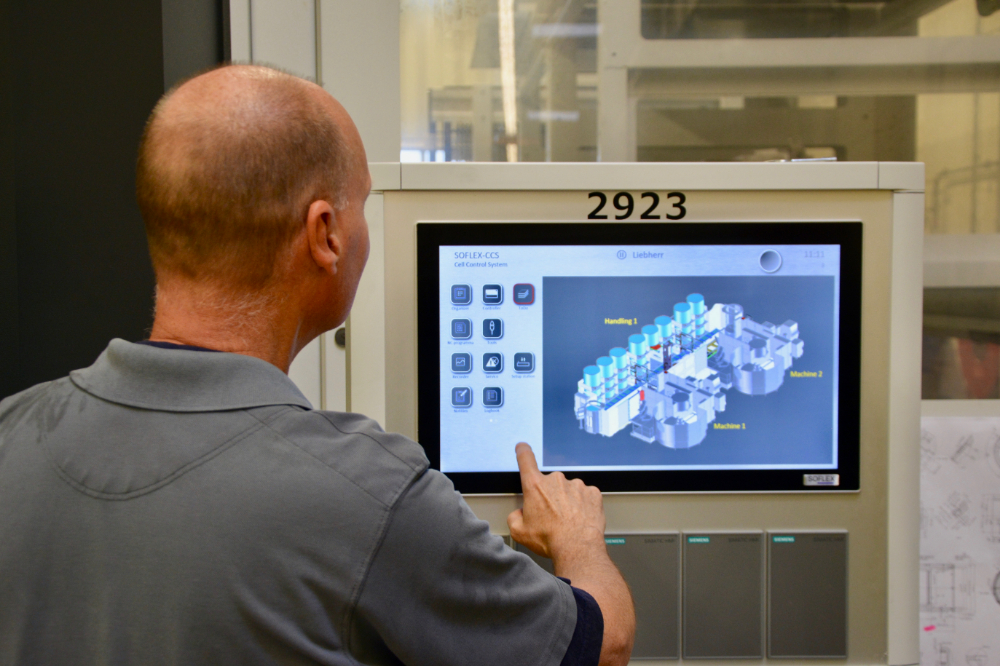
L'ensemble du processus est contrôlé par la plateforme Soflex.
Flexibilité
“De cette façon, l'opérateur choisit dans la bibliothèque les produits qu'il veut usiner, détermine l'ordre dans lequel ils doivent être fabriqués, et peut surveiller les processus à tout moment. Pour cela, il existe bien sûr un lien entre les positions des palettes d'une part et les fraiseuses, chacune avec ses propres outils et programmes CN d'autre part. Le robot est donc le 'maître', qui contrôle ses machines 'esclaves'. Cette plateforme nous offre une grande flexibilité entre les différentes commandes, ce qui est un autre avantage de taille“, poursuit Smits.
NOUVELLE METHODE DE TRAVAIL
Avec 24 positions de palettes maintenant disponibles, l'opérateur doit sans aucun doute passer beaucoup moins de temps à convertir les palettes.
D'autre part, son attention doit davantage cibler le contrôle de l'ensemble de la logistique: par exemple, il doit s'assurer que les outils sont ajustés à temps pour les prochaines heures de travail.
Productivité maximale
“En règle générale, nous commencions par couper les matériaux plus souples comme l'aluminium, car cela réduit le risque de bris d'outil et d'arrêts ultérieurs. Cependant, nous avons maintenant acheté une option dans l'unité de commande qui stocke automatiquement l'outil de découpe cassé, retire la palette de la machine et passe rapidement à la tâche suivante pour laquelle l'outil n'est pas nécessaire. Une technologie qui soutient ici aussi une productivité et une flexibilité maximales. A l'heure actuelle, nous pouvons faire fonctionner chaque fraiseuse environ cent heures par semaine, contre seulement soixante auparavant“, explique Smits.
Presse à copeaux
“Cela signifiait toutefois que nous devions également investir dans une presse à copeaux, car la poubelle se remplissait beaucoup trop vite et nous ne pouvions pas la vider la nuit. Les avantages sont que nous pouvons récupérer l'émulsion de refroidissement compressée, que nous obtenons un meilleur prix pour le matériau solide et que nous avons réduit le nombre de transports.“
EVALUATION
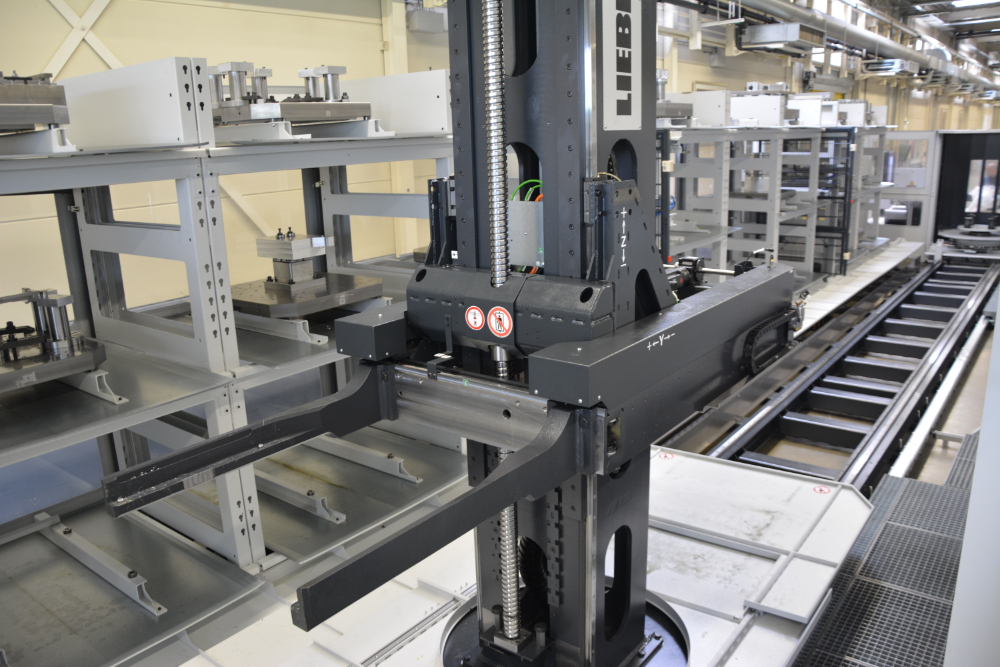
“Anticiper et déterminer correctement ce qui doit être fait pendant la journée ou la nuit, a pris un certain temps à certains opérateurs, mais entre-temps, tout le monde s'est finalement adapté. C'était tout un défi de permettre aux fraiseuses plutôt dépassées de communiquer avec un tout nouveau système de manutention. Hermle et Liebherr ont tous deux désigné un chef de projet allemand, en contact direct l'un avec l'autre. Non seulement ils se sont occupés des problèmes techniques liés au câblage et à l'interfaçage, mais Liebherr a également pris en charge le contrôle CE global de l'ensemble de l'installation. C'est différent des machines individuelles“, explique Smits.
Prêts pour l'avenir
“Dans l'ensemble, nous sommes très satisfaits de cet investissement. L'installation répond à nos attentes et en cas de problèmes, nous savons, grâce à notre expérience passée, qu'Ertec sera rapidement sur place pour toute intervention en première ligne. De plus, l'augmentation de la productivité des fraiseuses nous permettra de les amortir plus vite, mais nous tenions déjà compte de leur remplacement, lorsque nous avons opté pour ce système extensible. Nous sommes donc résolument prêts pour l'avenir“, dit-il encore.