- 12 mai 2023
- En Kevin Vercauteren
- | Source: Metallerie
Viaform optimise le processus de fraisage pour les petits diamètres
Un temps de finition réduit de moitié grâce à la spinjet d'Iscar
Si vous restez attentif aux innovations intéressantes et si vous pouvez compter sur le soutien d'un partenaire fiable comme Iscar, vous n'avez pas toujours besoin de débourser des sommes astronomiques pour franchir des étapes importantes. Le coût d'une Spinjet n'est rien comparé à celui d'une véritable broche à grande vitesse, mais les résultats sont similaires: des vitesses allant jusqu'à 55. 000 tr/min. C'est l'idéal pour les opérations de finition avec des fraises extrêmement petites. Et ces opérations sont fréquentes chez Viavorm, un fabricant de moules basé à Grammont.
Miser sur une plus grande diversification
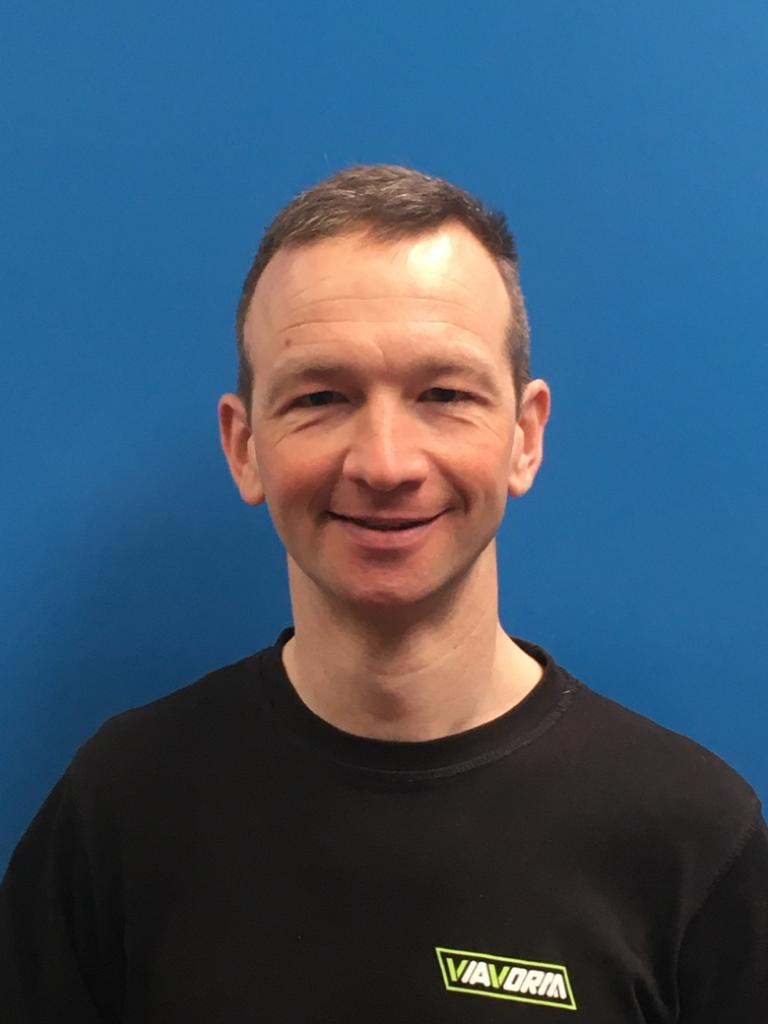
Viavorm est à l'origine un fabricant de moules. Plus précisément, de moules d'injection pour les pièces techniques. C'est du moins là que se trouvent les racines de cette entreprise fondée en 1969 à Grammont, qui est aujourd'hui dirigée par les deuxième et troisième générations.
"Bien que les moules fassent toujours partie de l'activité principale de l'entreprise, le marché a incité Viavorm à se diversifier davantage il y a quelque temps. "Nous pensions que le corona permettrait de revenir en arrière, du moins en partie, mais cet espoir s'est avéré vain. Les pays à bas salaires se taillent à nouveau la part du lion sur le marché des moules", déclare le coassocié Bjorn Lison avec une pointe de déception.
"En Belgique, il ne reste plus que les pièces les plus complexes. Lorsqu'il s'agit de prototypes ou de pièces qui n'en sont qu'au début de leur cycle de vie, on préfère les garder à portée de main au cas où il faudrait encore modifier le design. Nous fabriquons également de plus en plus de pièces de précision de ce genre en sous-traitance", poursuit-il.
Il s'agit souvent de pièces uniques et de petites séries d'une cinquantaine de pièces maximum. Néanmoins, Viavorm souhaite également innover dans ce domaine. En investissant dans une cellule robotisée, l'entreprise espère attirer des séries plus importantes. En même temps, c'est un moyen idéal de réduire les frais de personnel et de raccourcir les délais de livraison.
Des vitesses plus élevées
Les faibles tolérances sont typiques pour un fabricant de moules. Elles s'accompagnent souvent de vitesses plus élevées. Ces rotations supplémentaires sont particulièrement utiles pour les opérations de finition utilisant des petites fraises dont le diamètre ne dépasse souvent pas 0,2 à 4 mm.
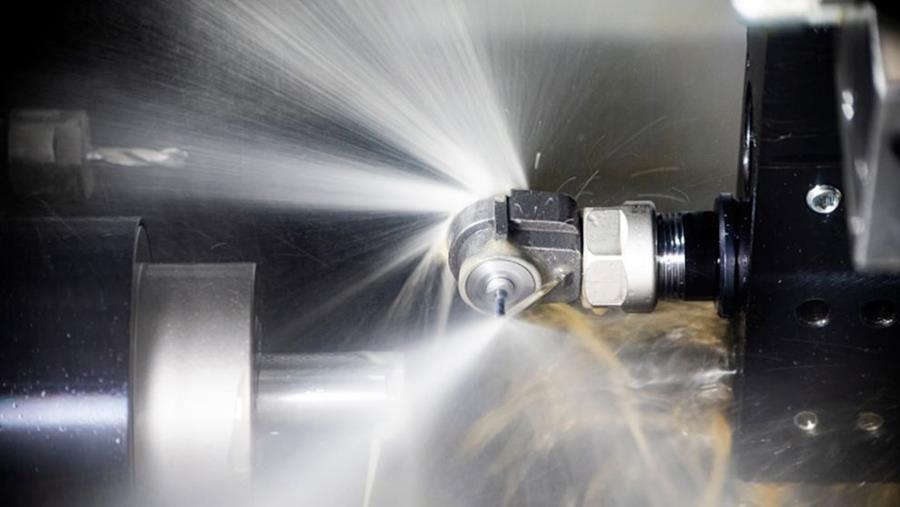
Viavorm est souvent confronté à ce type d'applications, mais les broches de ses fraiseuses Hermle atteignent une vitesse de 18.000 tr/min. Cela pourrait être bien plus, mais le prix est alors élevé. En outre, la protection de la broche ne fait plus toujours partie de l'équipement standard. Lison s'est donc mis à la recherche d'une solution alternative et c'est ainsi qu'il a découvert la Spinjet d'Iscar.
De quoi s'agit-il?
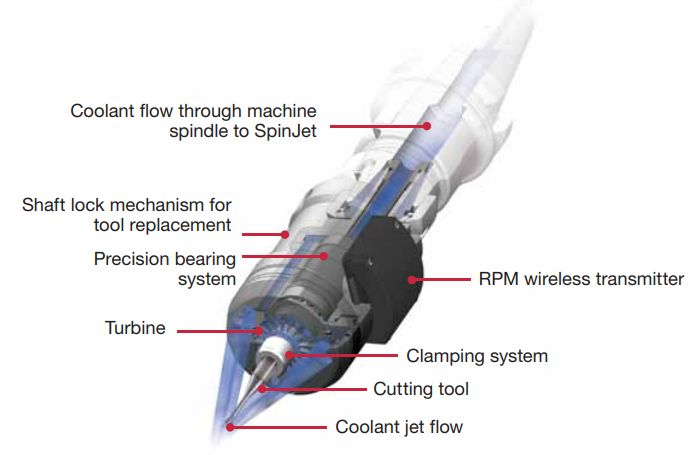
Spinjet est une technologie brevetée par Iscar, une broche supplémentaire qui s'adapte à la plupart des mandrins d'outil standard (HSK, SK, Capto, ER 32, BT...).
Le lubrifiant réfrigérant qui circule dans la broche met en mouvement une roue à turbine. Ainsi, en fonction du diamètre de l'outil, la vitesse peut être augmentée jusqu'à maximum 55.000 tr/min. Un signal sans fil de 2,4 GHz envoie la vitesse réelle à un récepteur fixé magnétiquement à l'extérieur de la machine. Ainsi, l'opérateur peut toujours lire le véritable régime en temps réel.
La Spinjet est compatible avec presque toutes les marques connues, mais nécessite une pression de refroidissement minimale de 25 bars (de préférence réglable).
Mise en service
"Dès que la question a été posée, Iscar nous a accompagnés dans ce processus du début à la fin", déclare le coassocié avec satisfaction. "On a calculé les gains de temps possibles sur base de différentes applications. Puis en tenant compte de nos vitesses de coupe moyennes, on a choisi le type de Spinjet le mieux adapté à nos besoins: Greenjet."
"En plus d'optimiser l'opération d'usinage, les vitesses plus élevées prolongent la durée de vie des fraises"
"Nous avons ensuite procédé à un essai sans engagement", explique Lison. "Ce processus d'essai est grandement facilité par le fait qu'on peut simplement télécharger sur le site la Spinjet et la géométrie 3D des outils afin de les intégrer de manière transparente dans son logiciel de FAO. Avec Cédric Delabarre d'Iscar, nous avons ensuite optimisé les paramètres de coupe pour que le processus soit parfaitement au point.
Évaluation
L'utilisation de la Spinjet offre un certain nombre d'avantages significatifs. "Tout d'abord, la broche de la machine peut être épargnée, car elle est mise au repos lorsque la Spinjet fonctionne. En outre, en plus d'optimiser l'opération d'usinage, les vitesses plus élevées prolongent la durée de vie des fraises. Enfin, les vitesses plus élevées permettent d'accélérer considérablement le processus de finition", ajoute Lison.
Dans le cas précis du travail d'érosion par enfonçage qui a servi de test - et qui, soit dit en passant, a également motivé l'investissement - la vitesse de coupe initiale de 70 m/min a pu être portée à 140. "Nous pensons donc pouvoir diviser par deux le temps de finition", ajoute Lison.